Y en a marre camarade !
Jean-Pierre SCHMIT
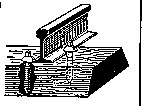
Toujours
les mêmes qui ont les honneurs. Le TGV Duplex (comme si cétait un appartement), le
TER (quelquefois une tortue), les trains containers (qui transportent quoi ? de
lair), Les CC, la CX (non, cest une voiture automobile), le quota de voyageurs
(comme si les usagers étaient du lait) tous ont les honneurs, mais moi, le rail !
Rien, le
néant comme si je nexistais pas. Pourtant ils auraient bonne mine tous ces
fringants sans moi.
En
remontant dans mon arbre généalogique, la famille " ornières " vers
1550 guidait déjà les convois équestres sur les dalles de pierres
Même à
lépoque de la Grèce antique, il existait déjà en Angleterre, la famille
" Madrier " de bois (un comté) allié avec les plaques de fonte (un
autre comté) assuraient plus récemment les mêmes fonctions de guides dans les mines (de
rien) de White Haven. Un membre de la famille vers 1763 (Richard Reynolds) nous fit
évoluer.
Nous
devinrent la famille " rail fonte ". Puis un autre génie
" Bessmer ", vers 1858, transformât lui aussi la famille et
nous devinrent " rail acier ". Mais on demande actuellement de
plus en plus à la famille. Nous avions la fonction de guider les véhicules et den
supporter la charge, et aujourdhui les sollicitations qui nous sont imposées ne
cessent de progresser. Lutilisation généralisée de rails longs et la surveillance
des phénomènes thermiques quelle implique, sont autant de contraintes qui exigent
une technologie de pointe sans cesse remise en amélioration. Notre évolution ne
sarrête jamais.
Cette
évolution est suivie par la Direction de lEquipement de la SNCF avec des
responsables à différents niveaux. Une coopération se développe sur le plan
international dans des groupes de travail de lIUC.
Les
progrès sont spectaculaires, quil sagisse de la création de profils lourds,
de lélaboration de lacier, du contrôle de la qualité ou de la définition
de nouvelles nuances applicables à un meilleur service des trains de plus en plus
rapides.
Du minerai
à la fonte
Le minerai
est surtout situé en Lorraine pour la France. Le bassin ferrifère lorrain sétend
à louest de la Moselle sur une centaine de kilomètres entre Nancy et le
Luxembourg. Il sest formé au début de lère secondaire. Le minerai lorrain
ou " minette " est oolithique. Le petit grain, de quelques dixièmes
de millimètres appelé oolithe est constitué doxydes de fer hydratés. Selon les
couches, la gangue qui aimante ces petits grains est plus siliceuse. Cette
caractéristique compense en partie le handicap de sa faible teneur en fer. Il faut
mélanger ces couches pour obtenir un " lit de fusion autofondant "
cest à dire un produit auquel il nest pas nécessaire dajouter de la
castine ou fondant pour réaliser les meilleures conditions de fusion dans les hauts
fourneaux. Les gaz dégagés par la fusion doivent pouvoir passer à travers le minerai
vers la partie supérieure du haut fourneau. Ils servent à réchauffer lensemble la
teneur en fer ne devant pas être inférieure à 30 ou 32%, rentabilité oblige.
Lextraction
se fait en trois temps
- forage
des trous qui recevront lexplosif
- mise en
place de lexplosif, mise à feu
-
évacuation du minerai (environ 100 m3 à la fois) par camion de 20 à 40
tonnes et bandes transporteuses.
Les
galeries dexploitation ont généralement 5 m de large et entre 2,50 et 10 m de haut
afin de permettre le passage des engins (pas de petits trains). Après exploitation de la
zone, les piliers de soutènement sont dynamités. Cest le foudroyage. Cet
effondrement, se propage jusquà la surface (bonjour les dégâts). La descente du
terrain est environ égale à la moitié de la hauteur de la galerie, doù
percussion sur le réseau hydraulique. Il faut pomper. Un mine produit en moyenne 3 à 4
fois plus deau que de minerai.
Le minerai
lorrain est presque épuisé. Il faut donc importer des minerais doutre mer (Canada,
Viet Nam, etc.) pour que les aciéries Sacilor continuent à tourner, doù leur
implantation en bordure de mer.
Le minerai
extrait ou importé est ensuite concassé, broyé, criblé, mélangé pour obtenir une
granulométrie ne dépassant pas 10 mm. Des combustibles (charbon maigre, coke
métallurgique, coke de pétrole) y sont ajoutés pour faciliter la combustion. Ces
opérations se font dans lusine dagglomération. Cet ensemble (minerai +
combustible) arrive dans un " modulateur " qui par brassage et
humidification sagglutine en formant des petites boulettes de quelques millimètres
de diamètre. Une chaîne sans fin fait passer le minerai pendant une minute sous une
hotte dallumage. Des brûleurs au fuel portent la couche à 1200°. Concassé,
criblé, il peut alors être acheminé vers le haut-fourneau.
Le Haut
fourneau
Cest
une cuve dacier dont lintérieur est tapissé de briques réfractaires. Il est
chargé par le haut, par des wagonnets (enfin !) spéciaux " skip "
(NdlR : " Skip " veut dire wagonnet en anglais, il serait
intéressant de savoir lorigine de ce mot). Sa hauteur peut atteindre 80
mètres, son poids 20 000 tonnes (la partie métallique de la tout Eiffel pèse 7 000
tonnes).
A sa base
se trouve le creuset de 5,50 à 8,80 mètres de diamètre. On y recueille la fonte liquide
et le laitier.
A 2,50
mètres du fond, le creuset est entouré de tuyères par lesquelles sont insufflés de
lair sur-oxygéné et le fuel aidant à la combustion. A cet endroit, la
température atteint 1900 à 2000 degrés.
Au sommet,
on trouve le " gueulard " qui comprend un sas dalimentation et
des dispositifs dévacuation des gaz.
Pour
refroidir cette masse et empêcher un échauffement excessif des matériaux soumis au feu,
il ne faut pas moins de 2000 m3 deau par heure. Les gaz de combustion de
faible pouvoir calorifique sont récupérés, nettoyés, lavés et envoyés dans les
cowpers. Ce sont des tours constituées intérieurement de briques qui emmagasinent la
chaleur dégagée par les gaz de combustion. Vers 1300° on coupe larrivée des gaz
et on souffle de lair extérieur à travers les briques. Cet air chaud sert à
alimenter le haut fourneau, cela explique quil faille au moins deux cowpers par haut
fourneau plus un de réserve.
La fonte
plus lourde se dépose au fond du creuset. Au dessus surnage le laitier (reste de
combustion). Un trou de coulée permet son évacuation. Si on injecte de leau dans
le laitier, il reste à létat vitreux. Ce produit finement broyé donne un
excellent ciment.
Le haut
fourneau consomme beaucoup deau, ce qui explique son implantation au bord de la mer
où leau est déssalée.
Ensuite on
ouvre le trou de coulée de la fonte qui est ensuite dirigée vers un wagon poche par des
rigoles. Ces wagons ayant la forme dun cigare ont une contenance de 200 tonnes de
fonte et possèdent 14 essieux.
Il faut
rappeler que le haut fourneau ne produit que de la fonte. La composition de celle-ci est
en moyenne de 93,37% de fer et 3,90% de carbone, 1,80% de phosphore, 0,50% de silicium,
0,03% de soufre, 0,40% de manganèse. Métal dur et cassant, la fonte résiste bien à la
corrosion, cest pourquoi, on le trouve dans la vie courante sous forme de
radiateurs, baignoires, plaques dégout, tuyaux, etc.
Mais la
fonte produite par Sacilor est dans sa totalité destinée aux aciéries pour être
transformée en acier par affinage. Lacier se distingue de la fonte par un taux de
carbone moins élevé. Ce pourcentage de 0,05 à 1% détermine sa dureté. Il contient
éventuellement des éléments spéciaux rajoutés, tels que le manganèse, le chrome, le
tungstène, le vanadium... Lacier est obtenu à partir de la fonte en fusion qui
dans laciérie va perdre la plupart de ses caractéristiques de fragilité.
Lacier
devient rail.
Cest
dans laciérie, installation aux dimensions gigantesques que seffectue
laffinage. Chaque acier doit répondre à des caractéristiques spécifiques pour
son utilisation, rail, ressort, carrosserie, charpente métallique, etc. Certains aciers
doivent donc être souples, dautres résistants à la traction, à la compression,
dautres encore durs ou malléables et souvent, ils doivent posséder plusieurs de
ces caractéristiques à la fois. La réalisation dun type dacier peut être
composé à la cuisson dun pot au feu. Lopération de transformation est
appelée " affinage ", au cours de laquelle, on ajoute des ferrailles
pour diminuer le taux de carbone. Différents procédés sont employés : Bessmer, Thomas,
et son dérivé LWS. Ils sont à notre époque obsolètes. Le procédé OLP (oxygène
lance poudre de chaux) fût mis au point en 1957. Il consiste à injecter du début à la
fin de lopération de l'oxygène dans un four à laide dune lance en
position verticale. De l'eau circule rapidement dans la lance longue de vingt mètres pour
assurer son refroidissement. La descente de cette lance dans le four sans pénétrer dans
le bain permet à certaines phases d'obtenir des réactions différentes. Sa capacité est
de 250 tonnes d'acier.
Le
procédé Kaldo
C'est un
convertisseur qui a une capacité de 240 tonnes, une sorte de four tournant sur lui-même
incliné sur son axe de 17° à une vitesse réglable pouvant atteindre 30 tours/mn. Une
lance à oxygène inclinable insuffle de l'oxygène pur à la surface du bain. Dans ces
conditions, l'oxygène soufflé se partage en deux parties :
- l'une
d'elles entre dans le bain et brûle le carbone,
- l'autre,
réfléchie, est brûlée et forme du gaz carbonique.
La
température produite par cette combustion est très élevée et la rotation du four a
pour effet principal de protéger le briquetage réfractaire supérieur. La voûte se
refroidit en communiquant sa chaleur au bain, ce qui nécessite un apport important de
ferrailles de récupération pour abaisser la température, ce qui est un avantage non
négligeable sur les autres procédés. La rotation du four a pour effet secondaire
d'assurer l'homogénéité du bain par le brassage qu'elle produit.
Le
procédé Kaldo le procédé le plus utilisé pour l'élaboration de l'acier destiné à
la fabrication des rails.
Cette
grosse "cuisine" où les fours sont hors de l'échelle humaine se réalise au
millième, voire au dix millièmes près. La présence de lhomme est discrète mais
que ferait-il dans cet enfer en fusion ? Il se fait aider par l'électronique qui assume
toutes les opérations. Des prises d'échantillons et de températures sont effectuées
régulièrement afin de rectifier si nécessaire en vue dobtenir les
caractéristiques demandées.
Quelque
soit le procédé utilisé, une fois l'opération terminée, deux produits se trouvent
dans le four : l'acier et la scorie.
La scorie
est évacuée par inclinaison du four et écrémage vu sa différence de densité.
L'acier,
à une température de 1500°C, est coulé dans des lingotières.
L'opération,
si elle est mal conduite, peut remettre tout en question. Pour fabriquer des rails,
l'habillage des lingotières est déterminé de façon précise, afin d'obtenir un acier
dit "calmé". Après solidification, le lingot est démoulé et envoyé au
laminoir.
Le rail
naît couché
Le lingot
est réchauffé à une température de 1200°C par des fours "Pits". Il y reste
de deux à seize heures selon sa température d'introduction. Lorsqu'il est "à
point", il est transporté très rapidement au "blooming". C'est une cage
composée de deux cylindres horizontaux tournant en sens inverses et réglables en hauteur
sur leurs axes horizontaux. Par des allers et retours et en diminuant l'entraxe, on
réduit la section du bloom qui s'allonge. Quinze à vingt-cinq passes sont nécessaires.
Il est ensuite décapé. Le bloom, cisaillé aux extrémités, long de 8 mètres, pèse
dix tonnes. Il est stocké pendant 8 jours environ afin de dégazer l'hydrogène dissous
dans le métal. Sans cette précaution, le rail risquerait d'avoir des fissures après
laminage.
Il est
repris et glissé dans un four de réchauffage au gaz naturel. La capacité du four est de
70 tonnes/heure.
A la
sortie du four, le bloom à 1200°C est dirigé vers un laminoir. Sa transformation
s'opère par passage du métal entre les rainures appelées "cannelures". La
forme du rail est complexe, il faut donc passer par des étapes intermédiaires. Le métal
épouse la forme définie par l'espace laissé libre entre les deux cylindres. Pour
économiser du temps, un nouveau système a été mis en place, c'est le train de
laminage. Le laminage s'effectue ainsi : sept passes dans les deux cages dégrossisseuses,
cinq passes sur le groupe cage universelle, enfin une passe sur la cage universelle
finisseuse. De nombreux contrôles sont effectués par des échantillons, contrôle de
qualité et caractéristiques du produit. D'autres contrôles sont effectués : examens
macroscopiques et analyses chimiques. Le rail passe ensuite à travers deux redresseuses
qui lui donnent la rectitude. Il est ensuite coupé à la longueur exacte, puis subit une
auscultation aux ultrasons. Enfin, les rails, au "coude à coude" présentent
leurs quatre faces. Un examen visuel minutieux les déclare "bon pour le
service".
Que de
chemin parcouru depuis l'extraction du bloc de minerai pour en arriver à ce rail que nous
connaissons bien, et que c'est joli deux files de rails bien alignées. Cela réjouit le
cur du ferrovipathe !
A titre
indicatif, nous publions un tableau de correspondances daprès les catalogues :
- O&K
N° 710 pour les hauteurs de rail et poids au mètre linéaire et
- PETOLAT
de 1922 pour les poids en Kg, le nombre de traverses par élément de 5 m et la charge
à lessieu acceptable, sachant que ces valeurs sont également relatives à la
nature du sol, lentretien de la voie, et lespacement des essieux.
Hauteur du
rail en mm |
Poids en Kg |
Nb traverses |
Charge à essieu Kg |
41 |
4,5 |
5 |
300 à 400 |
41 |
4,5 |
6 |
400 à 600 |
50 |
7 |
6 |
1000 à 1500 |
60 |
9,5 |
6 |
1200 à 1500 |
60 |
9,5 |
7 |
2500 |
60 |
9,5 |
8 |
3000 |
70 |
12 |
6 |
3000 |
70 |
12 |
7 |
3500 |
70 |
12 |
8 |
4000 |
? |
15 |
6 |
3500 |
? |
15 |
7 |
4000 |
? |
15 |
8 |
4500 |
98 |
20 |
? |
? |
125 |
30 |
? |
rail Vignole SNCF |
128 |
36 |
|
rail Vignole SNCF |
145 |
46 |
|
rail Vignole SNCF |
153 |
50 |
|
rail Vignole SNCF |
159 |
54 |
|
rail Vignole SNCF |
172 |
60 |
|
rail Vignole SNCF |
Plaque tournante |
1800 à 2000 |
Page
precedente